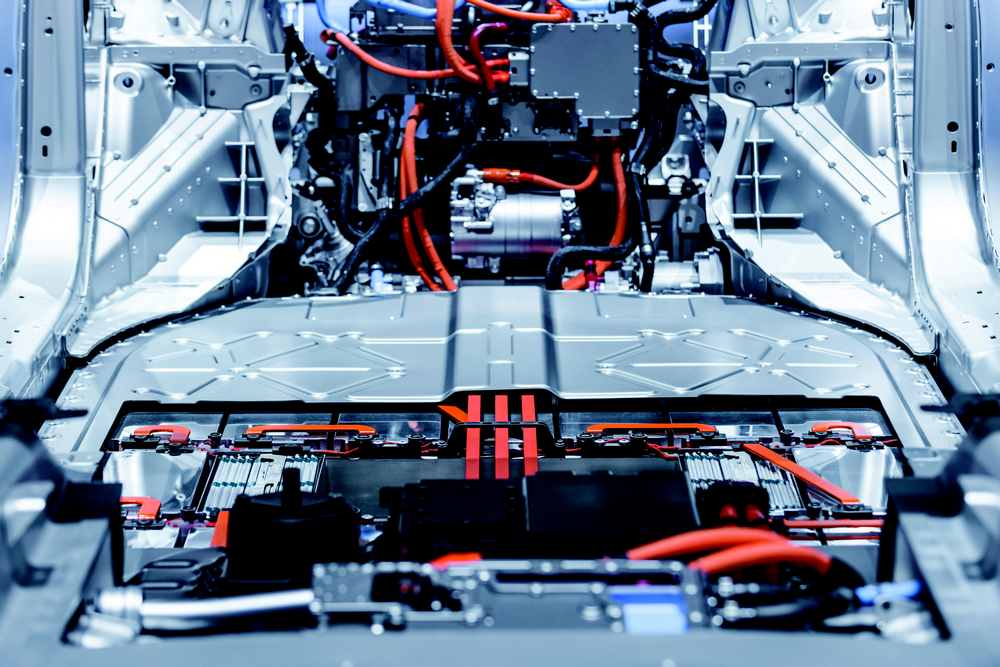
9/ Dunkrik at the heart of france’s battery valley
The major issue in the way of France’s aim to become carbon neutral by 2050 is reducing greenhouse gas emissions in the sectors with the highest emissions : energy (41% emissions), transport (24%) and construction (24%). Source : IEA, 2021, World Energy Outlook.
Electric car development seems to be one of the solutions to reducing these gases. However, the issue of the strategic metals needed to manufacture electric batteries and their end-of-life recycling is a hot topic.
In July 2023, the European Council adopted a new regulation that aims to promote a circular economy while regulating batteries throughout their life cycle. Specific recycling efficiency targets have been set at 80% for nickel-cadmium batteries and at 50% for other battery waste from now to the end of 2025.
The issue of reusing and recycling these metals and, more largely, the circular economy, is at the heart of e-mobility. The Hauts-de-France region, the leading automotive region in France with seven manufacturing sites, 800 businesses and 55,000 employees in the sector, particularly in Dunkirk, is moving in this direction with several large-scale industrial projects.
6 major projects in the territory : from battery production to recycling
In just a few years, Dunkirk has become the centre of France’s battery valley, which includes Verkor’s gigafactory for the production of battery modules (by 2025), Orano and XTC New Energy’s cathode production and recycling plant (by 2026) and Prologium’s solid state battery manufacturing factory (by 2026). More recently, Borax France announced a lithium conversion programme and Eramet-Suez is undertaking a recycling project. These facilities will complement the regional sector : ACC in Douvrin and Envision in Douai, located 80 and 120 kilometres from Dunkirk, respectively.
A total of almost 8.5 billion euros will be invested over the coming years in the port and industrial area to produce and recycle electric batteries (total power of around 64 GWh by 2030)
These battery manufacturers did not choose Dunkirk by chance.
The territory has many assets to its name :
- The 3rd largest port in France, boasting an excellent connection to logistics networks
- A strong industrial culture, a dynamic ecosystem
- Turnkey sites helping companies to get up and running quickly
- Effective cooperation between all the area’s stakeholders
- Raw materials (steel, aluminium) and low-carbon energy
170,000 tonnes per year of so-called “electrical” steel will be produced by ArcelorMittal at the Mardyck site from 2025, a project representing a €500 M investment. This steel is intended for electric motors in general and is characterised by its magnetic and mechanical properties.
60,000 tonnes of alloy ingots for the automotive sector will be produced by Aluminium Dunkerque from 2025. Aluminium is used to make vehicles lighter.
More aluminium is required for the production of electric vehicles than for the production of internal combustion vehicles.
The use of this metal, which is very light and a good conductor, is becoming greater and is now predominant in the construction of engine blocks and batteries. At present, Aluminium Dunkerque produces 40,000 tonnes of alloy ingots for the automotive sector and is aiming the increase this capacity by 50%. Of the additional 20,000 tonnes, a third will be made up of aluminium recycled from end-of-life vehicles.
Emmanuel Macron, President of France during his trip to Aluminium Dunkerque in 2023
Value chain for vehicle electrification
ORANO – XTC NEW ENERGY :
Expertise : Orano, an internationally recognised expert in the area of nuclear materials.
Project : Orano and XTC New Energy have signed agreements with a view to creating two joint ventures involving the production of cathode active materials (CAMs) and their precursors (P-CAMs) for electric vehicle batteries, as well as a shared R & D laboratory. When it comes to these two plants, which will be built on a 53 acre site in Dunkirk, the two industrial groups plan to have mirror-image shareholding and governance: Orano will hold 51% and XTC New Energy will hold 49% of the P-CAM plant, and XTC New Energy will hold 51% and Orano 49% of the CAM plant. These plants will primarily use NMC (a combination of Nickel, Manganese and Cobalt) technology, which is mainly employed in Europe and essential for the production and performance of electric vehicle batteries. Orano is also planning to set up and run a battery recycling factory on the same site near the P-CAM and CAM manufacturing facilities. This comprehensive project should help to create a complete and sustainable value chain in France and meet both France and Europe’s decarbonisation targets.
Completion dates : First commissioning: the CAM plant in 2026.
- 3 plants
- 1 R&D laboratory
- 53 hectares
- 1,5 billion € investment
- 1 700 jobs created
Against a backdrop of very significant electric vehicle growth in Europe, Orano and XTC New Energy are delighted that our project has been selected by the Grand Port Maritime of Dunkirk to host three plants for the manufacture of P-CAMs and CAMs and for recycling. This wonderful project should not only meet the needs of car manufacturers and gigafactories but also contribute to the creation of skilled jobs that will add value to a context where there are major challenges around the climate and industrial autonomy.
Thomas BRION Porject Director for the P-CAM and CAM plants in Dunkirk
Prologium :
Expertise : A global leader in the development and manufacture of the new generation solid state battery.
Project : Setting up a gigafactory for the production of solid state batteries for electric vehicles.
Completion dates : Work should begin by 2026, activities should be up and running in 2030.
- 5,2 billion € investmenT
- 3,000 direct jobs
- 180 hectares
- By 2030 the factory will have an annual capacity of 48 GWh, enough to power 500,000 to 750,000 electric cars per year
To accelerate the transition towards decarbonised transport, ProLogium is committed to introducing to the wider public solid state batteries combining exceptional performance, commercial viability and a reduced environmental footprint. Setting up a gigafactory in Dunkirk is key to this objective. Located in the “Battery Valley” in the Nord region of France, this production centre will benefit from low-carbon energies and, at the same time, from the power of this battery ecosystem and the talent of the Hauts-de-France region.
Vincent YANG, CEO and founder of ProLogium
Verkor :
Expertises : Low-carbon, high performance battery production.
Project : Setting up a production unit for electric battery modules intended mainly for the automotive sector.
Completion dates : Gradual commencement of activity in 2025 (1st phase), final completion in 2027
- 1,5 billion € investment
- 1,200 direct jobs
- 150 hectares
- 16 GWh of power developed by 2027
- 300,000 electric battery supplies for 300,000 vehicles per yeau
- 4 to 5 times smaller carbon footprint than batteries made in Chine
Since July 2020, Verkor has set itself a challenge : to accelerate low-carbon, high-performance battery production in Europe. Led by talented teams and committed partners, we are proud to be developing a more environmentally friendly model of mobility and, thus, driving forward the energy transition. After opening our Verkor Innovation Centre in Grenoble, the inauguration of our first gigafactory in Dunkirk ushers in a new chapter, work on which will begin this year. Our set-up in the Hauts-de-France helps us get involved in the creation of a new battery industriy-related ecosystem while integrating the whole value chain from material and equipment to recycling.
Benoit LEMAIGNAN, Co-founfer and CEO Verkor
Borax France :
Expertise : With a long-standing history in Dunkirk, Borax France converts boron oxides into speciality borates.
Project under review : The group is studying the feasibility of opening a line for the conversion of lithium, an essential component in the manufacture of electric batteries. Lithium carbonate would be refined into lithium hydroxide (12,000 tonnes per year) for dispatch to battery component manufacturers. The current study is looking at the best options for integrating the new service, in order to optimise water consumption and meet CO2 emissions reduction criteria.
Eramet-suez :
Expertise : ERAMET – SUEZ – Lithium-ion battery recycling
Eramet, Europe’s leading mining company and metallurgist, and Suez, a leader in circular solutions for water and waste, have chosen Dunkirk as their joint recycling factory for lithium-ion electric vehicle batteries. Production is due to start in 2025, subject to the final investment decision.
The two partners are combining their expertise: Suez specialises in the collection, sorting, preparation, dismantling and recycling of battery waste while Eramet deals with strategic battery metal recycling technology.
The aim of the project is to make Dunkirk the home of two facilities :
- An “upstream” factory for the dismantling and production of blackmass, a metallic concentrate of nickel, cobalt, manganese, lithium and graphite. Commissioning is set for 2025.
- A “downstream” hydrometallurgy factory for the extraction and purification of strategic metals from blackmass. Operations are due to begin in 2027.
- 50kt of battery modules per yeay, equivalent of 200,000 electric vehicle batteries
- 18 hectares